Glass
Glass: Translucent recycling process
Glass is mainly produced from sand, lime, and soda. The biggest advantage of this mineral material lies in the fact that it can be recycled many times over without any loss of quality. Thus, a new, full-fledged product can again come into being in an economic cycle, which additionally saves primary raw materials and energy.
An important contribution
to raw materials conservation
The elemental components used in glass production are not lost in the cycle.
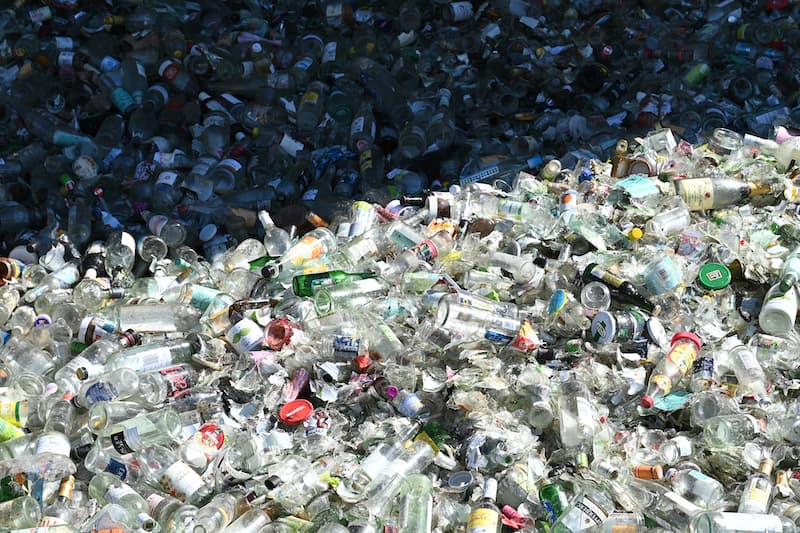
The cycle of glass is especially efficient
In Austria, a considerable part of waste glass is reintroduced into the cycle every year (e.g., approx. 317,000 tonnes of used glass, including 273,000 tonnes of bottles and other glass jars, are collected in 80,600 containers. Source: rundgehts). In addition to hollow glass bodies from households, broken sheet glass is very important. Some 85% of the collected sheet glass is recycled by trade and industrial companies, the remainder is disposed at collection points. An old window pane can easily be transformed into a new one.
Portion of old glass in percent 2019
Source: Bundes Abfallwirtschaftsplan 2022 Tabelle 34Glass production with a recycled content
Generally speaking, the sorting accuracy is an essential factor in the recycling of glass. After the crushing and sorting process, the glass waste is melted together with new raw materials and new glass vessels are produced. Sheet glass such as window panes, laminated glass (car windows), tempered glass, insulating glass, mirror glass or armoured glass is collected separately. Without adherent dirt and debris this glass can be processed for reuse. As a rule, this material is transformed into sheet glass granulate, which can be further transformed into many new products, among them new float glass or cast glass, glass vessels, glass fibres for insulation or reflective beads, as a truly brilliant example of boosting the safety of road traffic.
A primary focus on float glass
The sheet glass cycle for transparent float glass is particularly exciting. For producing float glass, the finely ground primary raw materials and glass granulate are melted at a temperature of about 1600°C. When the molten glass has cooled to approx. 1,000°C, the required final product can normally be formed. For producing float glass, clean potsherds are directly introduced into the production process. The sheet glass shards must not contain any contaminants, because the quality requirements applying to sheet glass are particularly stringent when it comes to transparency and visual qualities. To achieve the optimal shape, the glass is poured into a liquid zinc bath, which has an ideally smooth surface for hardening.
Thank you!
An error occured!
The user interface of this page is very complex, so it is easier to manage these functions on the desktop. We therefore do not currently offer a mobile-optimised user interface for this page.
Are you sure you want to perform this action?